安井行生のロードバイク徹底評論第11回 LOOK785 vol.2
目次
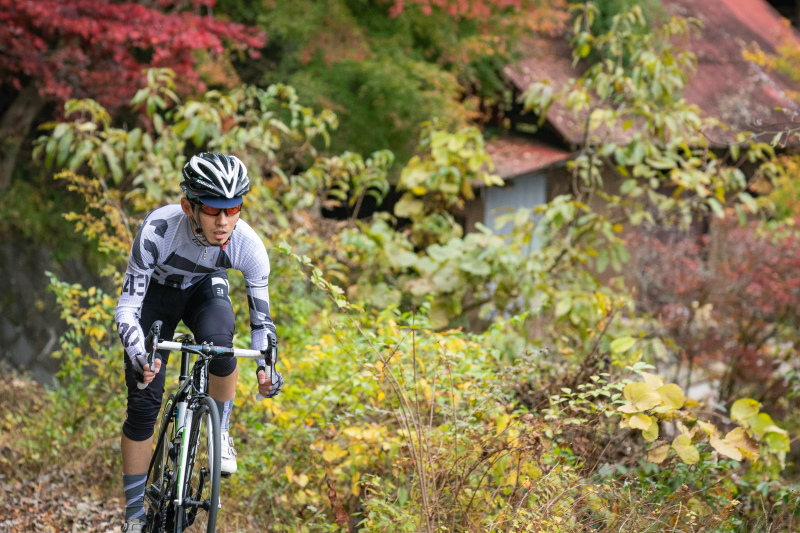
https://www.cyclesports.jp昨今の新型車の中で一頭地抜く注目を集めたルックのヒルクライムスペシャル「785」。同じく登坂を得意としていた名車585に惚れ込んでいた安井は思わず785ヒュエズRS、しかもZED2クランク仕様を買ってしまった。本国技術担当者のインタビューを交えながらお送りする、久々の自腹インプレ。
ここで一旦視点の高度を上げ、現在の市場における785の立ち位置を眺めてみる。
同価格帯でオールラウンドモデル、エアロロード、エンデュランスロードという3タイプをそろえることが常套手段となった現在、ルックは変則的なラインナップを敷いていた。
2017シーズンの商品構成は、一応、エアロの795、万能な695、エンデュランスの765ということになっていたが、695はデビューから7年も経つ老兵。前線に立って戦うには荷が重過ぎた(2018モデルで遂にディスコン)。765は完成車30万円前後のミドルグレードであり、価格帯がそもそも異なる。765のカーボンの弾性率を上げた765HM(後に改名し765RSに)はエンデュランスロードとして出色の出来であり、現在市場に存在するエンデュランスロードの中で数本の指に入る傑作だが、北米系ビッグメーカーのライバルと比べると存在感は薄かった(2018モデルでこれもディスコンに。残念)。
要するに、実質的にルックというブランドを牽引するのは変人795ライトRSと奇人795エアロライトRSという一卵性双生児。それはあまりに危うい一本足打法であった。そこにこの785が加わる。ラインナップのバランスを取るという意味でも785は機能するのだ。
しかし、商品構成を他メーカーと同工異曲(オールラウンド、エアロ、エンデュランスという3本柱)にしなかったところが共感を得た原因だろう。エアロの795とエンデュランスの765があるのだから、普通なら785は695の次世代機として万能モデルに仕上げるのが普通だ。しかしルックはそうしなかった。785のコンセプトを「軽量クライミングバイク」としたのである。
もちろん市場に登りが得意なフレームは多数存在するが、エアロも意識しつつ快適性も高めつつ……という没個性の万能モデルに仕立てられることが多い。上りに特化させたモデルは珍しいのだ。ライバル製品を横目で睨みつけた結果後追い商品ばかりになってしまった現代、潔い存在だと言える。
海外生産の理由
さて、背後に585の亡霊が見え隠れするとなれば、気になるのはフレームの構造だ。言うまでもなく585はカーボンチューブを無骨なカーボンラグで組み上げたラグドフレーム。595も同様。695や795は、外見上は段差などがなく一見モノコック風に見えるが、実はインナーラグを使って各チューブをつなぐという凝った手法を採っている。
その理由は、「ヘッド、シート、ハンガーは大きな応力がかかるので、剛性を高める必要がある。しかし、各チューブの中間部分には柔軟性を持たせたい。そのため、チューブの中間部分とヘッド、シート、ハンガーとで製法を変える必要があった。それぞれの部位で理想的な素材と製法を使い分けた結果、手間はかかるがインナーラグ製法がベストだと判断した」(本国開発担当者の弁)ということらしい。
では、785はどうなのか。結果から言うと、785は完全モノコックである。フレームの作り方で分類すれば、785は585や695ではなく、486や586の仲間なのだ。
10月末に台北で行われた795ブレードのプレスローンチ&試乗会に参加した際、ルック本社の技術担当者に785についても話を聞くことができた。ここからは彼のコメントをはさみながら文章を進める。
まず、785をモノコックにした訳を聞いておかねばならない。
「軽量性をなによりも重視したためです」。
シンプルかつ明快な理由である。ラグドフレームは、ラグ部分がどうしても二重になる。重量的には皮一枚のモノコックフレームが有利だ。
「フレームの成形にはEPSフォームの固形芯材を使用し、正確に加圧して無駄な樹脂を省いています(EPSは加熱・加圧時に収縮するため成形後に取り出すことが可能)」とのこと。
ルックにしては珍しく、使われているカーボン繊維の種類とその割合が公表されており、785ヒュエズRSは、ピッチ系炭素繊維を得意とする日本グラファイトファイバー(新日鉄住金グループ)のYSH-60A(60トン)が10%、東レのM46J(46トン)が13%、東レのT1100(30トン)が50%、東レのT700(24トン)が15%、アラミド繊維(12トン)が12%だそうだ(発表当初は90トンカーボンを使用しているとされていたが、どうやら間違った情報だったようだ)。
なぜこのような割合を公表したのかというと、60トンカーボンという高弾性糸をちゃんと10%も使ってるんだぜ、とアピールする意図があるのだろう。
「例えば60トンカーボンのプリプレグをほんの小さなピース一枚積層しただけでも、『我々のフレームには60トンカーボンが使われている』と謳うことができますからね」と担当者がニヤリとする。どこのメーカーを指しているのかは知らないが。
このように“60トンカーボン使用”と大々的に謳っている785だが、しかし60トンカーボンを使うことが目的ではなかったという。前記の通り、785ヒュエズRSは軽さを重視したフレームである。担当者はこう言う。
「60トンを使わなくても、作ろうと思えば785ヒュエズRSと同じ剛性・同じ重量のフレームは作れます。しかし、それにはプリプレグの積層位置の微調整がミリ単位で必要になり、レジンの選択がかなり難しくなってしまいます。それなら60トンを使って剛性と軽さを両立させた方が結果的に簡単だったということです。60トンを使いたかったわけではありません」。
ちなみに、YSH-60Aに関するある資料には、<高弾性ピッチ系プリプレグの採用によりフレームを675gまで軽量化できた一例>として、サーヴェロ・R5Caが載っていた。
795シリーズとは違い、785ヒュエズRSはアジアメイドだが、安直なコストダウンの策というわけではなく(もちろんそれも理由の一つだろうが)、この素材のチョイスも関係しているという。
「ご存知だとは思いますが、高弾性カーボンは非常にセンシティブな素材です(不用意に扱うと繊維が折れてしまう)。だから60トンカーボンを使い慣れているパートナー工場で製造しているんです。60トンカーボンを扱うのが得意な工場は限られていますから」。
軽く硬いバイクを作らねばならないという使命があった。60トンカーボンでそれが実現できるなら迷わず使う。そんな高級素材を使うからこそ、それを使い慣れている海外工場に製造を委託する。そういう判断である。